Introduction
In the fast-paced world of automation, control cables play a crucial role in ensuring the smooth and reliable operation of various automated systems. From manufacturing plants to transportation systems, control cables serve as the nerve center that enables the seamless communication between different components of an automated system. In this comprehensive guide, we will explore the importance of control cables in automation, the different types of control cables available, their key features and specifications, as well as best practices for selecting and installing control cables for optimal performance.
Importance of Control Cables in Automation
Control cables are an essential component of automation systems as they are responsible for transmitting signals and power between different devices such as sensors, actuators, controllers, and other components. These cables are designed to carry electrical signals, data, and power in a reliable and efficient manner, ensuring that the automated system functions smoothly and accurately.
In modern automation systems, control cables are used to connect various components such as PLCs (Programmable Logic Controllers), sensors, motors, and actuators, allowing for real-time monitoring, control, and feedback. Without control cables, it would be impossible to establish communication between these components, leading to system malfunctions, downtime, and loss of productivity.
Types of Control Cables
There are several types of control cables available, each designed for specific applications and environments. Some of the most common types of control cables used in automation include:
1. PVC Control Cables: PVC (Polyvinyl Chloride) control cables are widely used in automation systems due to their flexibility, durability, and cost-effectiveness. These cables are suitable for indoor applications and offer good resistance to oil, chemicals, and abrasion.
2. PUR Control Cables: PUR (Polyurethane) control cables are ideal for applications that require flexibility, high abrasion resistance, and resistance to oil, chemicals, and extreme temperatures. These cables are commonly used in robotics, automation machinery, and other industrial applications.
3. TPE Control Cables: TPE (Thermoplastic Elastomer) control cables are designed for applications that require flexibility, resistance to oil, chemicals, and UV radiation. These cables are suitable for both indoor and outdoor use and offer good performance in harsh environments.
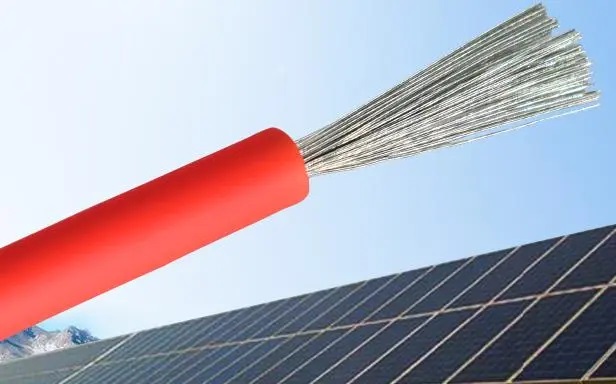
4. Composite Control Cables: Composite control cables combine different materials such as PVC, PUR, and TPE to provide enhanced performance in terms of flexibility, durability, and resistance to environmental factors. These cables are suitable for demanding applications in automation and robotics.
Key Features and Specifications of Control Cables
When selecting control cables for automation systems, it is important to consider the key features and specifications that will ensure optimal performance and reliability. Shielded cable with low inductance of the key features and specifications to look for in control cables include:
1. Conductor Material: The conductor material used in control cables can impact the cable's flexibility, conductivity, and resistance to environmental factors. Common conductor materials include copper and aluminum, with copper being the preferred choice for most applications due to its superior conductivity and durability.
2. Insulation Material: The insulation material of control cables is crucial for protecting the conductors from external factors such as moisture, heat, and chemicals. Different insulation materials offer varying degrees of resistance to environmental factors, so it is important to select a cable with insulation that meets the requirements of the application.
3. Shielding: Shielding is important for control cables used in environments with high electromagnetic interference (EMI) or radio frequency interference (RFI). Shielded cables help to minimize signal interference and ensure reliable communication between devices in automation systems.
4. Temperature Rating: Control cables are available in different temperature ratings to suit various operating environments. It is important to select a cable with a temperature rating that matches the ambient temperature of the application to prevent overheating and premature cable failure.
5. Flexibility: Flexibility is a key factor to consider when selecting control cables for automation systems that involve moving components such as robots and machinery. Flexible cables allow for easy installation and movement of components without risking cable damage or breakage.
6. Chemical Resistance: Control cables used in industrial environments may be exposed to oil, chemicals, and other harsh substances that can degrade the cable insulation over time. It is important to choose cables with good chemical resistance to ensure long-term reliability and performance.
Best Practices for Selecting and Installing Control Cables
To ensure the optimal performance and longevity of control cables in automation systems, it is important to follow best practices for selecting and installing these cables. Some key best practices include:
1. Assessing Application Requirements: Before selecting control cables, it is important to assess the specific requirements of the application, including the environmental conditions, operating temperatures, movement requirements, and potential sources of interference. This will help in choosing the right type of cable that meets the application's needs.
2. Consulting with Cable Manufacturers: Consulting with cable manufacturers can help in selecting the most suitable control cables for the automation system. Cable manufacturers can provide valuable insights into the different types of cables available, their specifications, and their compatibility with specific applications.
3. Proper Cable Routing: When installing control cables, it is essential to follow proper cable routing practices to prevent damage and interference. Cables should be routed away from sources of heat, sharp edges, moving parts, and other potential hazards to ensure their integrity and performance.
4. Using Cable Management Systems: Cable management systems such as cable trays, conduits, and cable ties can help in organizing and protecting control cables in automation systems. These systems help to prevent cable tangling, reduce the risk of damage, and facilitate maintenance and troubleshooting.
5. Performing Regular Inspections: Regular inspections of control cables are essential to identify any signs of wear, damage, or deterioration. Inspections should be conducted periodically to ensure that the cables are functioning properly and to address any issues before they lead to system failures.
6. Following Manufacturer Guidelines: It is important to follow the manufacturer's guidelines for installing, handling, and maintaining control cables to ensure their optimal performance and longevity. Failure to adhere to these guidelines may result in premature cable failure and costly downtime.
Conclusion
Control cables are a critical component of automation systems, enabling the seamless communication between different devices and components for efficient operation. By understanding the importance of control cables in automation, familiarizing oneself with the different types of control cables available, and following best practices for selecting and installing these cables, organizations can enhance the efficiency, reliability, and performance of their automated systems. With the right control cables in place, automation systems can operate seamlessly, leading to increased productivity, reduced downtime, and improved overall performance.